Sorting and classifying lines at C&D operations are as unique as fingerprints. Everyone has them. And they all are different. Just as fingerprints may have lines and whorls, sorting lines may have magnets and screens. It is how they all come together that makes them all special.
We turned to some of the more thorough C&D operations across the country for insights into why and how they classify C&D materials from wood to concrete by size.
The near-universal advice is to be practical about what sizes to produce from the get-go. That means comparing the yard’s production with the equipment you can purchase and get serviced at the front end with what the market demands at the back end.
“It’s an economics game,” says Barbee Cox, president of SB Cox Inc. The company operates at two locations—Richmond and Yorktown, Va. Although only 75 miles apart, they serve two separate markets with two quite different flows. The company receives a lot of plastics at Yorktown, little at Richmond, and takes in more wood in Yorktown than in Richmond. Cardboard is important in both locations, says Cox.
“We all need to produce a product that has some value to it,” Cox says. “The most important thing about any line is to produce what the end user wants.”
Both SB Cox sites have manual sorting at the top of the line. However, they do not preshred. “My theory is that it is easier to pull a bigger piece of material off the belt than to try to sort it small,” Cox explains. One day, however, he says he may install a high-torque shredder to handle some of the more contaminated wood debris.
“The biggest thing you get from preshredding material is it gives an even feed across the belt,” he says.
SB Cox has a trommel screen in Richmond, and Cox says he likes it, noting it does a better job for him than a fingerscreen. “We are pulling out the metal—the most valuable product,” Cox says.
Concrete, brick and block are segregated because the facility is set up to crush it. Segregating this material offers the advantage of getting the weight out of the residual material. Sending “heavies” to the landfill is a no-no for Cox.
Benjamin A. Harvey of E.L. Harvey & Sons Inc., Westborough, Ma., says, “We currently size to 1 inch minus, 12 inch minus and overs. Those were basically the sizes that would flow through the system based on the manufacturer specs and our specs.”
Harvey says the 1 inch minus gives the company a better ADC (alternative daily cover). “The 12 inch minus goes through an air classifier and a water bath, so that size seemed to move through the system better,” he adds.
Because of local market conditions, TnWaste, LLC, Knoxville, Tenn., does little material classification by size. However, it does sort by material.
“Right now, the only thing we are doing fractions on is the gypsum,” says Kim Kimmons, one of the owners at TnWaste. He notes that many of his customers are striving for “green” certifications, such as LEED (Leadership in Energy and Environmental Design), which requires sorting.
Head of the Line
TnWaste loads all of its C&D materials with an excavator. The material travels up an incline belt to an elevated picking line with eight stations. Each station sorts for a different material.
“We bale the cardboard,” Kimmons says. Plastic also is baled. Any unpainted, unadulterated wood is siphoned off and sent to a mulching facility.
Kimmons says the company follows a preset procedure with materials. Once the recyclable fractions are sorted, the material is containerized or baled. Then the cardboard is loaded on a flatbed truck and sent to a recycler who specializes in cardboard, and the wood is sent to another operation that specializes in mulching.
E.L. Harvey & Sons uses a trommel at the beginning of its sort line. This piece of equipment does both size sorting to 1 inch minus and 12 inch minus.
“We do not preshred but may look for this option in the future,” Harvey says.
Manual sorting is an important part of the whole operation for E.L. Harvey, but not in the sizing of materials. Manual sorters are material-specific, not size-specific, Harvey explains.
“Get the metal out wherever it is,” he urges those setting up a new line. “Just be very careful with a cross-belt magnet on the overs line. For safety reasons you don’t want big pieces of metal flying around the sorters.”
SB Cox uses a tub grinder for the chipping and mulching of its wood stream. “The size is based on the need of the customer,” says Merrill Baker III, environmental manager at SB Cox. The grinder has the ability to be adjusted to different screen sizes. Producing a clean end product is paramount, he says.
“Magnets are very important to me,” Cox says. “I need to have nails and screws out of the picking line.”
Cox had problems with his magnets pulling out every piece of trash that was attached to something metallic. He says he has not had problems with the cross-belt system installed at the Richmond location.
There are two magnets on the crusher at SB Cox: one on the main belt for one type of material and another on the remaining belt for other material. “The mulcher has one head pulley magnet for primarily nails and screws, etc.,” Baker explains.
“We had a cross-belt magnet when the line was initially installed,” Kimmons says. The problem was that the magnet worked too well.
If a wood roof truss with a dangling connector plate came up the line, the magnet would detect the connector plate and send the whole truss section to the metal box. Or, if a band of nails from a nail gun was rolled into some 6-mil poly plastic sheeting, the magnet would pick up the steel nails and send the whole wad of plastic to the metal box. “So,” Kimmons says, “we took it off.”
The company still uses an electromagnet at one of its locations.
Paying attention to rate of flow as well as to type of material also are important. “You want to make sure that the screened, sized materials flow through the system equally,” Harvey says.
Initially, Harvey says the company did not size wood scrap. “We shipped it to another processer,” he says. The company now sizes wood to 4 inch minus and then screens out fines. “This is strictly due to end markets,” he explains.
At most operations, incoming material is sorted out into specific stockpiles for processing. “Foreign debris, such as metal and trash, is removed from the stockpiles,” Baker says.
Over and Under
“In our system, sorting overs and unders just makes sense,” Harvey says. It divides the material and lessens the burden depth for the sorters.
Once the system was set up, it pretty much runs to the initial design, says Harvey, minus a few seasonal adjustments. “Besides running the system faster, we really don’t have much flexibility,” Harvey says.
SB Cox runs straight 1 inch by 2 inch for both boiler customers and mulch customers. Cox says material goes primarily to the boiler market, where it fetches $16 to $17 per ton. The mulch market, which pays around $25 per ton, is more attractive but tougher to get into, he says.
“I’m lucky that I can produce a material that will go either way,” Cox says.
That “luck” is the result of a lot of experimentation he has done with screens to fit each of the markets. That meant checking numerous lots as they came out of the grinder and determining which settings best fit the end-use.
“With the destoner, you definitely want over/under,” Cox says. “On the straight line, we have fines and everything else going across the line.”
Crushed concrete is produced to specification for the Virginia Department of Transportation (VDOT) for use as a highway subsurface.
“Richmond is on the fall line so it is not like demand is high or we get big money for it,” Cox says. Too much virgin stone simply is available. Instead, the company produces a spec product and barge it to the Tidewater region of Virginia, where demand is higher.
“We operate a portable Eagle concrete crusher, which is currently set up to screen two types of material,” Baker says. The crusher has the capabilities to adjust the screen to produce different sizes large or small.
Cox uses a computer program that was developed for the aggregates industry to produce the proper size product to spec. A Cat 330 pulverizer is used to processes the material into smaller sizes. Meeting that size requirement assures that the crusher can operate properly.
There are settings on the concrete crusher that control the size of material feeding into the screen. “The crusher manager determines the placement of the screens that will achieve the specifications of the customer,” Baker explains, adding that this may require several trial runs to achieve the specification requirements.
Most calculations required are based on historical data. “Crusher output is recorded on a daily basis and this data is reviewed to determine screen size and output requirements,” Baker says.
Any over/under classification at TnWaste is done at the customer’s request and it is an exception rather than the rule.
Not Making Millionaires
Margins are thin in all areas of C&D recycling. Even though Cox’ Richmond site is only 35 miles from a landfill he owns, he says he still wants to get 75 percent out of his stream. Labor is a factor, of course.
Each expert emphasized the need to serve local demand. A C&D operation in the Northeast, for instance, probably would find a good market for its residuals as daily cover. In the Richmond area, Cox is forced to treat residuals as trash even at the company’s own landfill.
Efficient operation helps, too. “Both the crusher and the mulcher have a variable speed control that controls the feeding of material,” Baker says. “Adjusting the speed down will slow production and conserve fuel.”
With tipping rates around $30 per ton, being able to sell recyclables at $20 per ton makes a big difference. “But it takes a lot of work to get the recyclables out of the stream,” Cox says. Still, he says he is happy with his investment and sees continued growth ahead. “This is not a fad,” Cox says. “Everywhere, there is increased pressure to recycle.”
The author is a freelance writer living in the Cleveland area. He can be contacted at curt@curtharler.com.
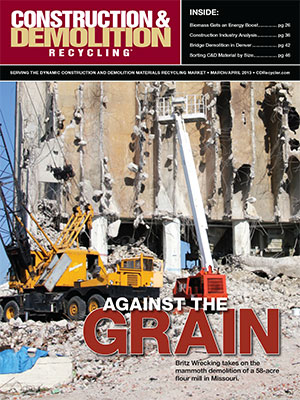
Explore the April 2013 Issue
Check out more from this issue and find you next story to read.
Latest from Construction & Demolition Recycling
- EPA announces $3B to replace lead service lines
- NWRA honors award recipients during annual breakfast at WasteExpo
- Safe Fleet, ITA Dynamics unveil integrated financial, route management system
- Bateman unveils 210 series orange peel grapple
- Republic reports first quarter growth
- Meridian Waste completes second acquisition of 2024
- NEPA revisions could delay critical infrastructure, ABC says
- Liebherr USA announces new divisional director