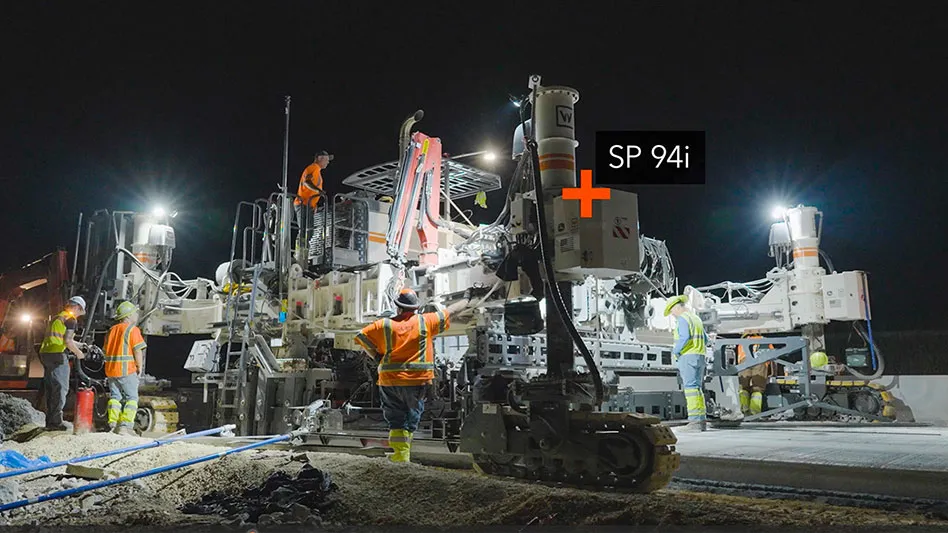
Photo courtesy of Wirtgen Group
To reconstruct the eastbound lanes of Interstate 44 in Missouri, Capital Paving & Construction took out the old concrete and repaved it in two segments. The first segment was 19 feet with a 12-foot drive lane and a 7-foot shoulder. The second segment was 22 feet wide with a 12-foot drive lane and 10-foot shoulder.
When Capital Paving & Construction was awarded the work to repave the 8 miles of I-44 in Rolla, Missouri, the company knew it would need the right equipment for the task. “On this project, we knew we were going to have access issues and there would be no room for a traditional dowel basket,” says Ryan Porter, senior project manager for Capital Paving & Construction. “That prompted conversations on how we could work differently on I-44.”
Capital Paving & Construction, based out of Jefferson City, Missouri, is a third-generation family-owned business bringing years of experience, quality work, safety and commitment to each job site. When looking for a new machine, they contacted the Germany-based Wirtgen Group to see one in action before making any purchasing decisions.
After seeing the machine at work on a job site in California, Capital purchased a Wirtgen SP 94i Slipform Paver for this project. This SP 94i has a dowel bar inserter (DBI) that will help them work more efficiently despite their limited access issues.
“Instead of putting the basket out in front of the paver and dumping the trucks over top of it, the DBI inserts the dowel bars right behind the mold,” says Tyler Kirchhoff, a foreman for Capital Paving & Construction. “It makes it easier on the crew and easier for the dump trucks to get back and help out.”
This also helps with labor and efficiency on the job site.
Capital chose to add the TCM 180i to the paver as well. The TCM 180i or Texture Cure Machine is a self-propelled unit that produces the desired surface textures on the freshly paved concrete surface. This machine has a modular machine design that makes it possible to adapt to working widths between 13 feet, 1 inch and 59 feet, which is what the Capital team needed to keep working efficiently.
Productivity also comes down to the support users receive from the Wirtgen Group.
“The support from Wirtgen has been wonderful,” Kirchhoff says. “We set up the DBI at the shop and the Roland team worked with us to bring it back out to the site and reconstruct the paver out there and got it set. They fought the rough time with me for that week and we got everything squared away to where I understood it more and we were good to go after that.”
Latest from Construction & Demolition Recycling
- USTMA announces Tire Recycling Foundation
- New York landfill owners accused of permit violations
- Biden-Harris administration touts clean construction materials progress
- Stellar debuts NXT68 hooklift at WasteExpo
- Metso now offers diesel-electric Lokotrack models
- Green Mattress Recycling hires new CEO
- Collapsed Baltimore bridge brought down with chain of explosives
- Volvo CE broadens services commitment with minority stake in fleet software developer