
Upgrading a construction and demolition (C&D) processing facility can take a large amount of time, effort and money. When JKS Ventures, Melrose Park, Illinois, decided that it was time for a full upgrade, General Manager Sherri Clementi made sure it was prepared for the process.
“It just got to the point where I was rejecting companies because we were too full and we couldn’t process it,” Clementi says. “We decided we needed to invest in a new system or we wouldn’t keep up in the area. With the new system, we can process more efficiently, accept more [customers] dumping and handle more volume.”
JKS Ventures, a sister company to D&P Construction was the first C&D recycler in the Chicagoland area, according to Clementi. The outdoor facility sits on 13 acres and accepts a wide range of materials from concrete and brick block, landscaping debris and scrap metals. There are more than 150 employees between both companies.
“We have our own baler to ship [out materials]. We grind wood and sell colored mulch to both landscapers and wholesale. We pulverize and sell our dirt. We crush concrete. We’re a wholesaler as well to a landscape transfer facility, which can supply with various types of mulch, stone, and dirt,” Clementi says. “We do a little bit of everything—ferrous and nonferrous recycling, sorting baling.”
The company also makes products from clean concrete at its concrete crusher facility.
EXPANDING THE VOLUME
With its old system, JKS ran 10 to 11 hours per day with more than 20-year-old equipment, and it was difficult to process its entire stockpile.

The old system included a conveyor line, six hand sorters and an Action finger screener with the original intention of processing material only brought in by the company. “We couldn’t keep up with the capacity and volume,” says Clementi.
Clementi had heard of Process Dynamics Co., an equipment representative based in Big Rock, Illinois, through trade shows and referrals from other companies. After making initial contact, she and set up a meeting with Gary Petersen, Process Dynamics sales engineer.
“They came to our facility, and with them being a local company, we realized it would be a great fit for us and our company for parts and services,” Clementi says.
Process Dynamics began shipping out the equipment in summer 2016, but the first thing that was updated at JKS was the property’s landscape.
“With the new system came new land improvement,” Clementi says. “We needed to replace concrete, get new electric boards and the house over our pickers. We had to go through a custom building (process) of a house over our hand sorters, which was a huge investment as well.”
Once the landscaping was completed, an A and B line system designed by Sherbrooke OEM, Sherbrooke, Quebec, with key pieces including large finger screens manufactured by General Kinematics (GK), Crystal Lake, Illinois, was put in place. Dick Reeves, GK director of resource recovery, says installation of the fully automated line took six to eight weeks.
Petersen says the system was designed to handle 125 tons per hour or 1,000 to 2,000 tons per day during an eight-hour day of typical C&D debris processing.
“The system is fed by a grapple, and it’s the grapple operator’s responsibility to provide good, uniform feed and to discard things that will damage the system,” Petersen explains.
The two large finger screens, operating in tandem, separate 8-inch overs that go to the alpha line for hand sorting. The sorters remove wood, concrete, ferrous metals, old corrugated cardboard (OCC), plastics and any other materials JKS wants to sort to keep and maintain.
The B line holds the minus 8-inch material. It goes through magnetic separation where ferrous metals are pulled out, and is sent through another finger screen to remove minus 1½-inch materials. Any other material goes through a GK Triple Knife De-stoner.
Reeves says the De-stoner is developed to drop out the heavy materials, such as brick, concrete and large pieces of wood, from the lighter weight materials to reduce the weight going to landfill.
“The system receives a lot of volume and separates it into three different streams—heavies, such as rock and dense materials; medium materials such as wood; and ultra-lights such as plastics, light material and thin paper,” Petersen says.
One hand sorter is placed on the heavies line to grab anything that isn’t rock or brick. JKS has eight bunkers where rock, nonferrous metals, contaminated and quality wood are stored. At the end of the system, a compactor accepts the waste from the A and B lines.
“(JKS) just purchased a new compactor and trailers that are compatible with the compactor,” Petersen says. “It’s an automatic system that works great and is high capacity. It was equipment that they weren’t used to—big, heavy and needs to be understood—and they’re understanding it very well right now.”
The new system has allowed JKS to process more materials from outside haulers and the company since expanded its fleet to 50 trucks.
ON THE UP AND UP
Reeves says the system has been running for about a year, and “they’re processing way more materials now than ever before.”

“They used to have piles of material, but they’ve gobbled that up, and now they can just process everything they get in,” he says.
Since upgrading was complete, Clementi says the biggest benefit is being able to accept more debris again. She says the De-stoner installed in the new system results in four to five clean loads of concrete and is helping JKS divert more from landfill than before. “We were disposing a lot of those little stones in the landfill, which was a lot of weight for us, and now we’re getting them out,” she says.
With the new system in place that includes a compactor at the end of the line, Clementi says new trailers were needed that were compatible and allow for more material to be hauled to the landfill in one trip. “We have a whole new way of doing things now,” she says.
Petersen says this system has put JKS a step ahead of the game in the area. “The Midwest is really late in catching on with this kind of recycling, especially in comparison with the East Coast,” he says.
Clementi says increased volumes are the biggest benefit, allowing the company to get back to business.
“It’s not so much expanding the scope, it’s the volume we can now accept,” Clementi says. “Now we can take the big demolition contractors, which we couldn’t handle before. Now that we’ve invested all this money, land and space, we can open up many more companies to dump here, and that’s been a big help.”
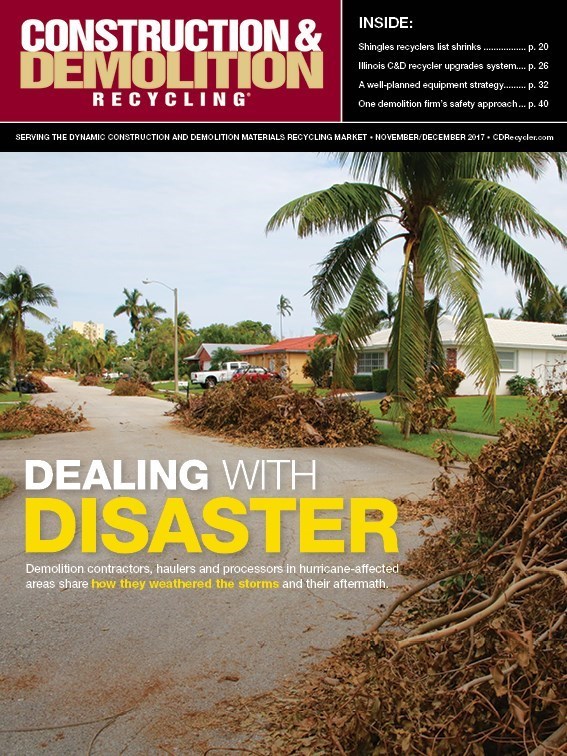
Explore the November 2017 Issue
Check out more from this issue and find you next story to read.
Latest from Construction & Demolition Recycling
- Brokk opens new Canadian distribution center
- EPA announces $3B to replace lead service lines
- NWRA honors award recipients during annual breakfast at WasteExpo
- Safe Fleet, ITA Dynamics unveil integrated financial, route management system
- Bateman unveils 210 series orange peel grapple
- Republic reports first quarter growth
- Meridian Waste completes second acquisition of 2024
- NEPA revisions could delay critical infrastructure, ABC says