
Buildings are incredibly resource and material intensive, accounting for more than one-third of global resource consumption and 11 percent of global emissions stemming from their construction, renovation and demolition, not accounting for operations. Moreover, most of these building materials are lost to the landfill when buildings and interior spaces are renovated or demolished. According to the U.S. Environmental Protection Agency (EPA), demolition activities alone accounted for more than 90 percent of the estimated 569 million tons of construction and demolition (C&D) waste generated in the U.S. in 2017. This was more than twice the amount of municipal solid waste (MSW) that the EPA estimated was generated in the same year. And this type of waste generation has been growing, quickly, ever since the EPA first estimated C&D waste generation at 136 million tons in 1996.
Certainly, not all C&D waste is attributable to buildings: by weight, most is generated from roads, bridges and other infrastructure in the form of asphalt, concrete and other aggregates. The EPA calculates that buildings themselves are estimated to account for just 32 percent of C&D waste by weight, but this category is more problematic than others because of the types of materials it generates. Much of the road, bridge and other infrastructure-related waste is primarily comprised of asphalt (which boasts an impressive recycling rate of 99.7 percent) and concrete and other bulk aggregates, which have an 85 percent recycling rate. The materials in buildings and their interior spaces, however, often fall into the mixed C&D category, which achieves a significantly lower recycling rate of only 37.6 percent, according to the Construction and Demolition Recycling Association (CDRA). Mixed C&D recycling, therefore, is an industry sector that poses significant opportunity for growth.
With so many mixed building materials headed to the landfill, the U.S. does itself a disservice in allowing these valuable resources and their associated embodied carbon and energy to leak from the country’s resource and economic system.
So, why has the recycling rate of these materials remained so low in comparison to asphalt and concrete? The issues are multifaceted and span the value chain, including manufacturers, designers and architects, construction contractors, materials processors, and the public policy officials and waste managers in local and state governments. Building a better solution will require us to use systems thinking principles and shift our perspective from the linear to the circular.
C&D waste from a designer’s point of view
I spent the first part of my career in the architecture and design industry. I always did my best to deliver design solutions that met my clients’ needs while also being sustainable. But there were often many competing demands and numerous variables to consider, including functionality, aesthetics, materiality, availability, sustainability and cost. And apart from the select manufacturers that have developed internal recycling programs for the products they produce, designing for reusability and recyclability was not a readily discussed topic. From the architect’s perspective, commingling the C&D waste for collection and hauling off-site was the construction contractor’s responsibility. Sometimes, if the contractors were pursuing Leadership in Energy and Environmental Design (LEED) certification, the construction contractor would need to ensure that at least 50 percent, or sometimes 75 percent, of materials were diverted from waste. Where this material went after that, or how it was processed, was anyone’s guess.
By and large, the design community has not had to think about what happens to building materials after they leave a building site as waste. LEED, launched in 2000, has evolved over time and grown from one certification standard to a suite of certification options. LEED remains the most popular certification option in the U.S., but there are now other competing building standards including Green Globes, which advertises itself as a more flexible competitor to LEED, and the Building Research Establishment Environmental Assessment Method (BREEAM), an international standard that evaluates the whole lifecycle of the built environment. But here’s the challenge: As far as building materials are concerned, these standards have historically focused primarily on the impact of the materials on indoor air quality and, to a lesser extent, the sustainable sourcing and manufacturing of materials. With few exceptions, less attention has been paid to products’ full lifecycle impacts, including end of life management.
For example, prior to LEED version 4 (which was not fully phased in until late 2016), commercial construction projects could achieve a maximum of only two possible, non-mandatory points related to C&D waste: one point for achieving 50 percent waste diversion and the other for achieving 75 percent waste diversion. LEED version 4, now updated to LEED version 4.1, maintains these same essential waste diversion benchmarks and also gives more options to incentivize material reuse and products being taken back by the manufacturer via extended producer responsibility (EPR). It also made mandatory the development of a C&D waste management plan for these projects but requires few specifics within the plan beyond identifying five material streams to be targeted for diversion. There is still no incentive to achieve more than 75 percent waste diversion, and a given project does not necessarily need to achieve this level of diversion to attain LEED certification at any level based on the other points earned.
I do believe the LEED system has good intentions, however, it also has its weaknesses. LEED’s weaknesses have not gone unnoticed by others in the industry, particularly others who seek higher levels of sustainability standards and compliance. Since its release in 2006, the Living Building Challenge (LBC) has sought to achieve environmental restoration through the built environment by producing more energy than is consumed for given projects, treating water on-site and using healthy building materials. LBC’s version 4.0 standards for waste are rigorous. These standards seek to achieve “net positive waste,” both by diverting 80-100 percent of all waste and by reusing materials that would otherwise become waste. Its waste management plan, which is referred to as a “materials conservation management plan,” must address the entire project lifecycle from design through end of life. The other LBC requirements are no less rigorous, and consequently, its strength is also its weakness: Only 24 buildings in the world have achieved ”Certified Living” status for meeting these benchmarks.
Two other certification programs deserve mention here: TRUE Zero Waste (an acronym for Total Resource Use and Efficiency) administered by Green Business Certification Inc., and Underwriters Laboratories’ (UL) Environmental Claim Validation Procedure 2799 for Zero Waste to Landfill. The TRUE program focuses on holistic organizational change to minimize waste and is ongoing over an organization’s life. The UL certification is used to demonstrate landfill diversion rates of 90 percent or higher, commonly from facility operations such as manufacturing, although it can also be used to certify time-limited events such as concerts and conventions or even construction, demolition and renovation projects. While these programs are unique in that they are exclusively focused on waste, the scope of these programs—TRUE encompassing the organization as a whole and UL focusing on operations only— makes them unlikely to become the program of choice for most architecture and design projects.
This leaves LEED as the industry’s de facto certification option. On top of LEED’s general lack of emphasis on C&D waste mitigation and management, the responsibility for achieving these goals is effectively placed on the construction contractor to procure a service provider and produce the correct documentation to meet the LEED standard requirements. What’s more, there is no consideration in LEED or its directly competing standards for designing for the ease of reuse or recyclability. Frankly, the design industry just isn’t thinking about what will happen at the end of material life. And if the design industry isn’t thinking about it, and isn’t asking manufacturers to create products that cater to these needs, the result is a vast disconnect between how and what we are putting into our buildings and the ability to reuse or recycle these items at the end of their initial lives.

Our role in the waste & recycling industry
Stakeholders in the waste and recycling industry, whether it be consultants, processors or public officials and program managers, have a duty to communicate how the C&D recycling process works. This is not limited to outreach to the design industry.
GBB is currently working with a client as its C&D materials recovery coordinator to help achieve a goal of zero C&D waste during renovation projects. At the start of one project, the need for these services was particularly evident during an early visit to a construction site. It became clear that the construction contractor wanted to help the client meet its goal, but was unaware of what was and was not recyclable, how the materials were processed and what the contracting team could do to ensure recyclability. It appeared as though the construction contractor was dependent on someone else later resolving the issue of recycling. In fact, in the years since LEED was introduced, the responsibility has indeed fallen on the C&D recycling service provider to document materials and diversion percentages on reports that are submitted to the contractor, who submits the reports to the design team, who then submits the documentation package to the certification body. At every level, there is a disconnect from the next. This is not a best management practice.
Logistics can also be challenging for construction contractors. A well-run C&D recycling facility with a relatively automated processing system may not have much trouble achieving 50 or even 75 percent waste diversion, depending on the incoming material stream. But achieving more diversion than 75 percent can be challenging, especially considering some of the specialized building materials that have been developed in the past few decades. Because of this, there is a growing demand for C&D facilities to update and expand processing capabilities to include materials that some may consider difficult to handle. If a C&D recycling facility is not equipped to handle such specialty materials, the contractor must devise a way to manage multiple material waste streams at the construction or demolition site, which may be space or cost prohibitive and require a higher level of training to all crew members.
Salvaging materials
We have a responsibility to communicate and collaborate across the value chain, as well as to challenge ourselves to keep improving and innovating. This includes, at the policy and public program management level, how we communicate about C&D waste. In direct opposition to how it is commonly referred to, C&D “waste” is actually a valuable resource that should be recovered and not placed in landfills. Rather than speak in terms of C&D waste management, which implies that we are burdensomely managing something of little to no value, we should speak in terms of C&D materials recovery, which better represents the reality that we must recover these valuable resources to the greatest extent possible. A similar difference exists between the words “demolition” and “deconstruction,” which are two fundamentally different activities. Demolition implies destruction such that the components of a building will be rendered unusable for any purpose and can only be recycled or landfilled. Deconstruction, on the other hand, involves dismantling a building with the goal of maximizing the salvageability and reuse of its components. This is a paradigm shift that starts simply with how we talk about the idea of waste.
To incentivize this paradigm shift through innovation and increased recycling, some jurisdictions have taken inspiration from the various sustainability certification programs and made C&D waste management plans and diversion minimums the standard requirement—not the option. This could be accomplished by making these requirements a building code minimum, a condition of permitting or a means for building owners and builders to avoid citations or fines, such as CALGreen’s green building standards code, which requires that all construction projects divert at least 65 percent of waste and either submit a waste management plan or use the services of a company that can provide verifiable diversion documentation. Some local jurisdictions have even higher diversion minimums. Policy could also be written to require proof of recycling in order to receive a conditionally refundable deposit, as is the case in the cities of San Jose and Santa Monica, California.
To meet a similar end, policy could revolve around certain C&D materials prohibited in landfills, such as metals, gypsum board, clean wood, concrete and stone, and the requirement that all C&D materials pass through a recycling facility prior to landfilling, as in King County, Washington. Other types of financial disincentives to wasting materials exist, such as through landfill taxes or fees. For example, North Carolina taxes both MSW and C&D landfills and taxes MSW and C&D transferred to states for out-of-state disposal. Landfill requirements for C&D materials are not as stringent as for MSW, often leading to lower construction and management costs, and therefore, lower tipping fees that do not necessary serve to incentivize the diversion of C&D waste.

Technology to move from recycling to upcycling
Recycling C&D materials at high rates today is possible, but the industry needs to ensure it is continuing to make strategic investments in its infrastructure. Similar to municipal MRFs, there is not one prototypical C&D recycling facility that can serve as a model for all others. All facilities are different and have differing considerations for future investment, but investment is key to keeping these facilities operating at maximum efficiency. C&D recycling facilities should be receptive to feedback from the customers and communities they serve to ensure they meet evolving needs. By weight, most of today’s mixed C&D materials can already be diverted from waste, either for recycling or beneficial reuse, at a well-equipped C&D recycling facility. There are many reasons why this may not occur, as discussed previously, but the industry should not let insufficient equipment be one of them.
As building information modeling (BIM) technology has continued to develop and mature over the past decade, the architectural and design industry can document exactly what materials go into a building as part of its construction plans, down to the manufacturer, material type, shape, size and color. This could be an additional tool used and required for building permit submission as we plan for the future of building de- and re-construction. This is the concept of buildings as material banks. Indeed, buildings are rich stores of materials, whose embodied energy, carbon and economic value should not be lost due to a lack of planning, communication and collaboration. Certainly, recycling is better than landfilling, but better yet is upcycling to create something of higher value.
One of the biggest barriers to building material reuse is the unknown (i.e., not knowing exactly what materials may be available, what its structural properties are, and its current condition). Ascertaining this information requires time and money, ultimately disincentivizing material reuse and conservation. Today’s technology helps remove this barrier. If we document today the components of a given building project, we can better understand how to salvage and reuse these components in the future. If we could reach a tipping point of having enough projects planned in this manner, we would have a critical mass for the creation of a materials exchange, where materials from buildings are aggregated for sale to the reuse market. Implementation of such an idea may be years away, but it is possible now.
C&D materials recovery gives back so much. These processes create more jobs than landfilling the same materials, lengthen the life of our landfills, save our limited natural resources and preserve the embodied energy and carbon that was required to mine or harvest virgin resources and produce the building materials in the first place. Thanks to advances in BIM technology, we can know all the construction materials that go into a building, and in turn, anticipate its materials for recovery at the end of its useful life. And through proper C&D materials recovery coordination, we can work together to make connections and foster collaboration across the value chain, communicate to bridge the disconnects where they exist between actors, and create a system that works hard to preserve the value of materials by keeping these products circulating within, instead of leaking out of, our economy.
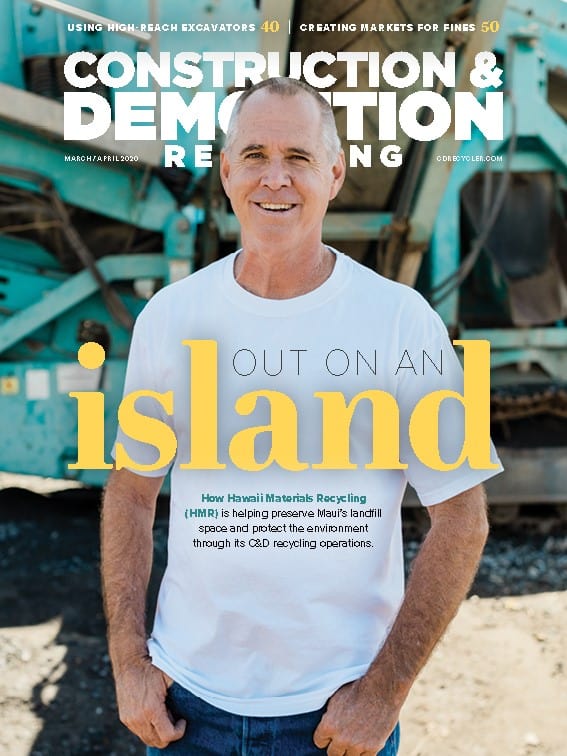
Explore the March April 2020 Issue
Check out more from this issue and find your next story to read.
Latest from Construction & Demolition Recycling
- Connect Work Tools names new service manager
- Architects’ billings slow, contractors stay busy into summer
- RMDAS figures show ferrous still in a trough
- Mt. Diablo receives RCI certification at Pittsburg, California, C&D facility
- Plastics recycling company wins top prize at NextCycle Colorado Pitch Competition
- Arena-sized venue is demolition target in Alabama
- Brandt scrap handlers available through Murphy Tractor
- Hendrickson celebrates Tiremaax installation milestone