
Sun Services in Beltsville, Maryland, has served the waste and recycling needs of customers throughout Maryland, northern Virginia, eastern West Virginia, southern Pennsylvania and Washington D.C. since 2004. Specializing in commercial disposal, residential demolition recycling projects and construction dumpster rental, their team relies on streamlined operations to increase efficiency and maximize production.
Determined to capitalize on its thriving hauling operation, Sun Services constructed a new C&D recycling plant in October 2013 to better leverage the value of the materials it collected.
The company designed the 28,000-square-foot plant on five acres to house all material loading and processing under one roof to comply with local ordinances. Once material enters the plant, it is weighed prior to being dumped for a LEED inspection. The material is then loaded onto the sort system where it is sized and separated into 2-inch-minus, 2- to 6-inch and 6-inch-plus pieces. Larger pieces comprised of ferrous and nonferrous metal, concrete and aggregate, wood, plastics, cardboard and residuals are then filtered out. The valuable materials are recycled while the residuals head to a local waste-to-energy facility to be processed.
Originally, Sun Services loaded material to be recycled straight onto a metering table with a three-deck screen, while difficult-to-recycle material was set off to the side to be landfilled. The material from the line would then be sorted by hand. This initial configuration left a lot of contamination reduction to be desired, according to Sun Services President Brian Shipp.
To help design a plant that was capable of processing material in a more efficient manner, Sun Services partnered with Notre Dame, New Brunswick-based Sparta to help conceptualize and build a recycling facility better able to meet its needs.
Shipp says his team started discussing the merits of introducing a new shredder on the front end of the line a couple years ago to help better size incoming material. After ongoing discussions, they settled on investing in the Pri-Max PR6600 from Wilsonville, Oregon-based SSI Shredding Systems. Capable of processing between 60-150 tons per hour, this low-speed, high-torque industrial primary shredder is able to shred, tear, crush and reduce materials that would otherwise be impossible to size with Sun Services’ previous equipment.
“We added the SSI shredder on the front end of our line seven months ago, which has doubled our throughput in a 10-hour day,” Shipp says. “It makes everything a uniform size, breaks up all the stuff that is tied together and allows us to take materials we wouldn’t be able to take before, such as railroad ties. It has streamlined that process a lot.”
Shipp says that thanks to the shredder, Sun Services doesn’t have to be as judicious in choosing which materials to process and which to send directly to landfill for expediency.
“We used to have to justify what of our incoming material was worth processing, but now, thanks to our shredder, we just put everything through our system,” Shipp says. “Where before we would receive a load of (mostly) carpet and discard the entire load, now we’ll run that through our system. Even if it only produces a couple pieces of metal, it’s material that we didn’t have before. Plus, we’re able to get the dirt, dust and other small stuff out as well during this process.”
After this material is sized, it is separated onto the facility’s A and B lines consisting of 6-inch-plus and 2-inch to 6-inch material, with 2-inch-minus being collected off of the latter. The A line with the 6-inch-plus has a belt that runs underneath it to collect wood waste. To process this wood, Sun Services installed a Rotochopper grinder two years ago that is fed by the facility’s centrally located conveyor.
Conversely, the B line is fed through an air separator that helps distinguish between lights and heavies. The plant runs a cross-belt magnet on the B line as well to pick up any metals that have found their way through the system. Remaining heavies are collected to be used for haul roads at a nearby rubblefill.

Reduced maintenance
Besides the benefit of helping double the plant’s throughput, Shipp says the recent addition of the SSI shredder has been significant in helping reduce downtime and promote cost savings, specifically when it comes to belt life. Because everything is getting uniformly sized with the new equipment, larger debris is no longer placing undue wear on these service items, which has significantly cut down on belt replacements.
“We have two incline belts that come off of our screen that are rubber-cleated,” Shipp says. “We probably pay around $20,000 a belt, and we were replacing these roughly every six months before. We replaced them right when we put our SSI shredder in seven months ago, and they’re still fine. We think we might be able to double their service life. Additionally, our main sort belt would take a beating with our previous setup. The transition of material from the incline belt to the main sort belt was about 5 feet. Sometimes you’d get a piece of concrete that was the size of a 5-gallon bucket falling that distance, which can do a lot of damage. But with the new SSI equipment, that can’t sneak through. That’s one of the reasons our main belt has lasted as long as it has with just minor maintenance.”
Continued improvement
Shipp says that Sun Services’ recent retrofits are just the tip of the iceberg for what the company has planned in the future.
The company just put in a 5,000-square-foot addition on its plant, which is pending inspection, to help alleviate some of the congestion that came with the cross traffic of having the material dumping and processing operations conducted in close proximity under one roof.
“This made our traffic pattern convoluted when we were trying to load a trailer—there was cross traffic between the loader loading the trailer and trucks backing in to dump,” Shipp says. “This caused problems since our plant’s inception, but we dealt with it. However, as this place saw a substantial increase in traffic, we put this addition on to change where our trailers are loaded, and in doing so, added another scale so that the trailer on the scale can get loaded to the exact weight every time to improve the productivity of the truck and trailer.”
Due to more space being allotted by the new configuration, the company plans to do more screening and refining of its fines to collect more material and open up new end markets.
“Instead of having a 2-inch-minus product that has a lot of dirt, trash and aggregate, we’ve purchased a Nihot air separator and are looking into sourcing a screen at the moment. Obviously, fines are a big headache for those who work in this industry, and we’re just trying to get ahead of that,” Shipp says.
Shipp says the SSI shredder will allow the company to put a magnet on the A line, which wasn’t possible before due to the diverse size of material that was running on the belt. Once this magnet is in place, Sun Services will perform additional fines testing before investing in screening equipment and determining end markets for the material.
Shipp says that while the company’s new investments have transformed how the C&D recycler manages its waste, Sun Services will continue to invest back into the business as long as there are opportunities for improvement.
“We’re still early in the process of having adopted new equipment, but just looking at our general productivity, it’s gone way up—which is what we were hoping and expecting to happen,” Shipp says. “Being able to process double the material in the same amount of time has been huge. We have the mindset that we need to constantly evolve. Once we’re done with this upgrade and the next, I’m sure there will be something else on the horizon.”
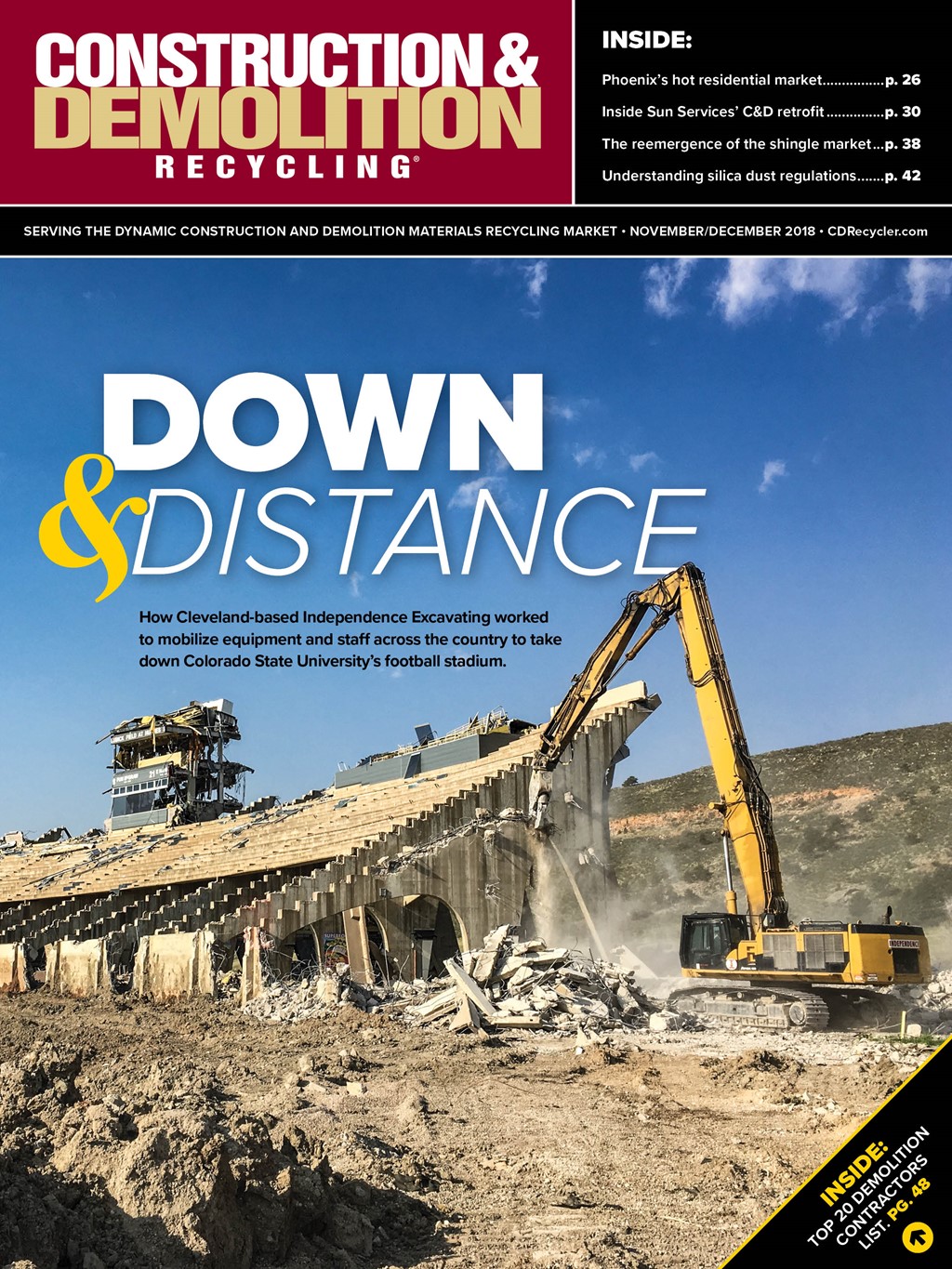
Explore the November December 2018 Issue
Check out more from this issue and find your next story to read.
Latest from Construction & Demolition Recycling
- Connect Work Tools names new service manager
- Architects’ billings slow, contractors stay busy into summer
- RMDAS figures show ferrous still in a trough
- Mt. Diablo receives RCI certification at Pittsburg, California, C&D facility
- Plastics recycling company wins top prize at NextCycle Colorado Pitch Competition
- Arena-sized venue is demolition target in Alabama
- Brandt scrap handlers available through Murphy Tractor
- Hendrickson celebrates Tiremaax installation milestone