

Since its start in the 1960s, doing the right thing has been a core value for Dem-Con Cos. The third-generation, family-owned business provides diversified, full-service recycling, processing and disposal from its facilities in Shakopee, Minnesota. The company entered the construction and demolition (C&D) recycling space in 1985 when it began recycling wood. Dem-Con later added a C&D material recovery facility (MRF) in 1999.
Dem-Con’s C&D MRF processes a variety of materials, including wood, ferrous metals, nonferrous metals, aggregates, cardboard and shingles, but wood makes up the largest portion of what it processes at about 20 percent. Dem-Con President Bill Keegan adds that it is one of the highest value products processed, as well.
“Wood is the primary component in this waste stream,” he says.
The company receives its wood from the C&D waste stream, as well as from various pallet waste sources. However, Keegan says the inbound stream of wood has “dramatically changed” in recent years. “We have less recoverable wood than we had in the past,” he says. “We are seeing more composite and constructed wood materials, such as glue laminate beams, trusses and sheet board, which is reducing the amount of recoverable wood in the C&D waste stream.”
Treated and manufactured wood is not recyclable and has to be sent to landfill, he adds. “We are currently about 50/50 for manufactured/dimensional lumber,” Keegan says.
Dem-Con used to process about 40 percent manufactured or treated wood five years ago, he says. That figure also includes composite wood and plastic building materials that are nonrecyclable.
“We are not aware of any end markets currently for the manufactured wood, but we remain open to considering viable end markets if they become available,” he says.
“As far as reducing what goes to the landfill, one solution would be using less manufactured wood, but that goes against current building material trends,” Keegan adds.
Despite the evolving inbound stream, he says Dem-Con is still processing enough wood to meet end-market demands.
An evolving process

When Dem-Con established its C&D MRF in 1999, the company relied primarily on hand sorting C&D loads from the facility’s transfer station. Over the last two decades, Dem-Con has upgraded the C&D MRF to improve efficiency and decrease reliance on manual sorting as finding workers to perform this job has become much more difficult in recent years.
“There is still a decent amount of manual sortation for our wood stream,” he says, “but securing labor continues to be a significant challenge. [The] Minnesota unemployment rate just hit 2 percent, which further exacerbates these challenges, impacting the ability to effectively operate the facility.”
Automating the sorting process allows the company to reduce its reliance on manual sorting and enables those workers to take higher skilled labor positions at the MRF facility instead, he adds.
Dem-Con’s C&D MRF features a C&D processing line from Erin Systems Inc., a business unit of Premier Tech Systems of Canada, that was added in 2008, along with a stationary electric grinder from Rotochopper, St. Martin, Minnesota, followed by a Rotochopper hammermill that feeds directly into the wood storage and loading building. The company also uses augers to automatically load trailers with wood products in a storage facility.
Keegan says Dem-Con added the 40-foot-by-60-foot storage building about five or six years ago to protect high-quality wood products from the elements, thereby reducing moisture.
“There were rejections of material on the biofuels side for moisture content, so if we could keep material dry, it had a greater value,” he says. “Also, you can’t sell wet animal bedding. So, keeping [the wood] dry was beneficial for all markets, for material handling and quality of the product, making sure it didn’t have mold or degradation,” Keegan adds.
Dem-Con added an air classifier to its C&D MRF two years ago as a way to reduce reliance on manual sorting. The air classifier helps to sort smaller fraction C&D materials that are difficult to sort by hand.
“We’ve gained operational efficiency,” Keegan says of adding the air classifier. “We’ve been able to essentially have less labor and process more material.”
The company also added air handling equipment to control dust in the wood grinding and sorting areas about six years ago to clean things up and to help improve efficiency.
Keegan adds that Dem-Con is continually evaluating ways to automate the C&D MRF. He says, “We’re looking to things like robotics, opticals and automated sortation for wood processing.”
An evolving market
End markets serve as the main driver for recycling any commodity, including wood. Over the years, key markets for Dem-Con’s wood have included biofuels, animal bedding, landscape mulch, erosion materials and sorbents, with these markets fluctuating based on demand.
As with equipment, end markets for wood have evolved. Until a couple of years ago, Dem-Con primarily sold its wood to the biomass market. Keegan says that end markets for wood have diminished in Minnesota in the last couple of years, though.
“We have seen some biomass plants in Minnesota closing down or moving away from recovered wood as a feedstock in favor of green wood or agricultural waste products based on the price point for these products,” he says. “Wind and solar are also becoming the desired choice for renewable energy, further driving some biomass markets to shift away from recovered wood.”
Although the biomass market has declined in Minnesota, Keegan says other end markets for wood remain strong. “Our larger focus is on animal bedding and landscape mulch, with some limited use in sorbents,” he says.
Regardless of end-market changes, Keegan says Dem-Con will continue finding ways to recycle wood and other C&D materials.
“It’s easier and more profitable to landfill materials, but at the end of the day, we are recycling materials to conserve our air space and landfills,” he says. “That’s really the genesis of C&D recycling—do the right thing and have a sustainable business operation. That’s what drives us and why we have had this facility running since 1999.”
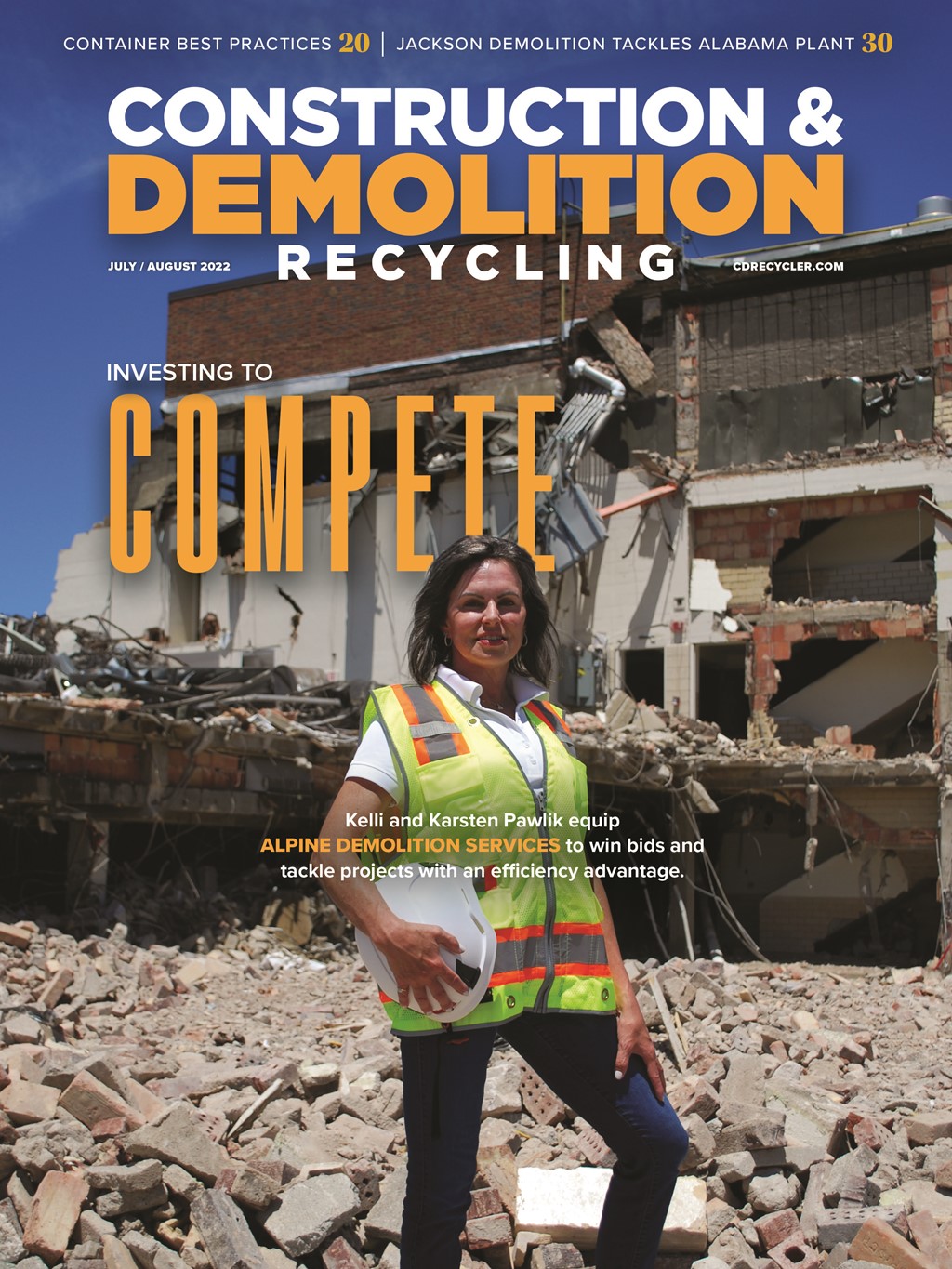
Explore the July August 2022 Issue
Check out more from this issue and find your next story to read.
Latest from Construction & Demolition Recycling
- Connect Work Tools names new service manager
- Architects’ billings slow, contractors stay busy into summer
- RMDAS figures show ferrous still in a trough
- Mt. Diablo receives RCI certification at Pittsburg, California, C&D facility
- Plastics recycling company wins top prize at NextCycle Colorado Pitch Competition
- Arena-sized venue is demolition target in Alabama
- Brandt scrap handlers available through Murphy Tractor
- Hendrickson celebrates Tiremaax installation milestone