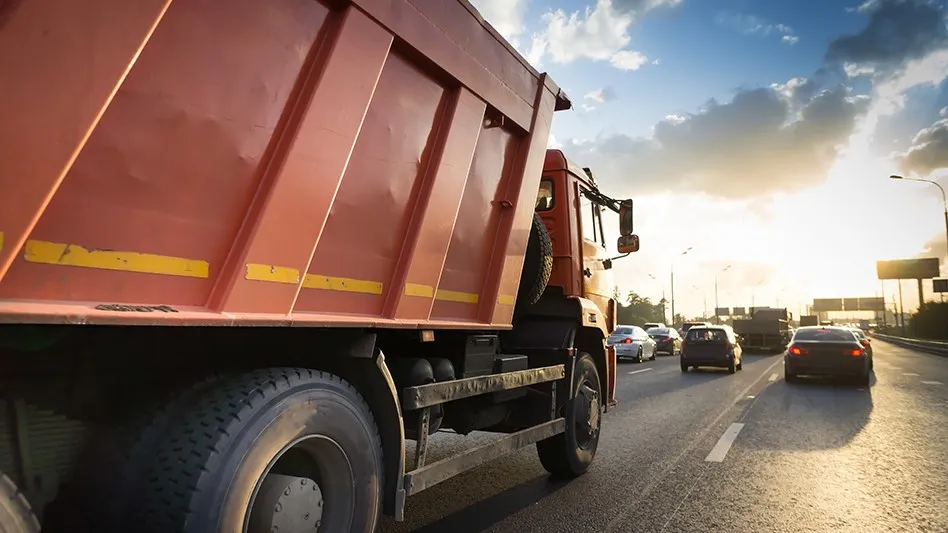
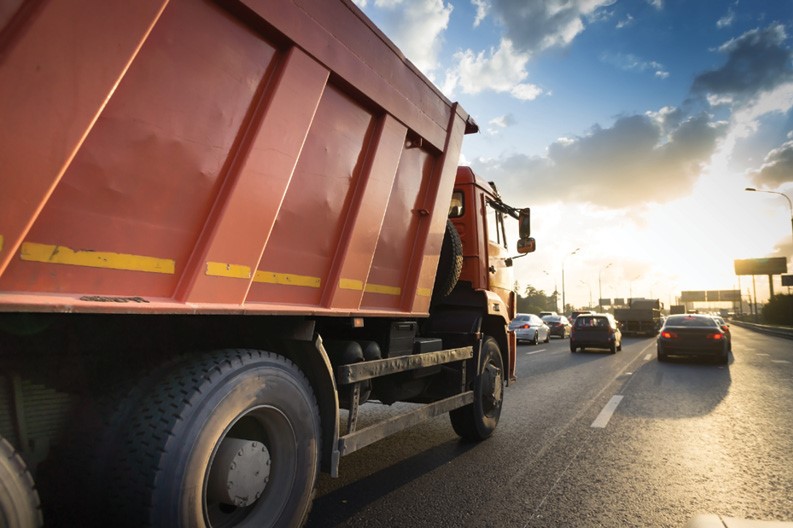
Stormwater runoff is often a leading cause of stream impairment in urban areas. Given the large variety of materials typically hauled away from construction sites for recycling, the excess deposits from roll-on and roll-off containers can be a significant contributor to the volume of water that ultimately ends up in local streams, lakes, wetlands and rivers.
This can cause flooding and erosion and wash away critical habitats for organisms living in the stream. To help better protect the environment, container manufacturers are required to deliver on a robust list of regulatory standards from government entities.
From United States Department of Transportation (DOT) guidance to requirements under the National Association of Corrosion Engineers, the regulatory requirements outline what needs to be achieved with the end product while also leaving room for companies and municipalities to control how these containers ultimately prevent stormwater runoff.
As long as the end product prevents stormwater run-off, the container remains compliant. The overall waste industry should ensure proper due diligence to prevent stormwater runoff and protect natural resources.
Standard operating steps can minimize dumpster water pollution in stormwater runoff, such as keeping the lid closed to prevent rain entry, positioning dumpsters away from storm drain inlets, avoiding the disposal of liquids in a dumpster and replacing the unit when it begins to rust or crack. However, the real work begins with the container itself.
Keeping design in mind
Companies have the opportunity to be innovative with product development. While there are known measures that minimize contamination, the responsibility begins with the provider’s design and engineering.
While company leaders launch corporate responsibility programs to hold themselves and their clients accountable, developing new products to meet compliance standards is critical.
By creating products and a standard of behavior that show respect for the environment, companies can support the circular economy by sourcing responsibly, reducing carbon footprints and developing more products with environmental benefits. Charlotte, North Carolina-based Wastequip has pursued this idea through the development of a new roll-off cover with a permanent mount that opens to both sides of the container. The dual-locking system is designed to prevent unauthorized dumping. In addition, the UV-protected polyethylene cover provides an impact-resistant outer shell designed to withstand extreme weather conditions. Features such as these collectively can combat the risk of unwanted matter getting inside the container, ultimately resulting in less pollution in stormwater runoff.
City and state governments also can regulate the design of containers used to collect and transport waste and recyclables.
Many municipalities in the Northwest no longer allow containers with inside drains. Prohibiting drains in containers continues to be a popular trend, expanding to other areas of the country, as well.
Roll-off container manufacturers adhere to local design rules during the design process and specialize in adjusting the engineering to provide a final product that suits both the client’s needs and the requirements of these local regulations.
Testing the waters
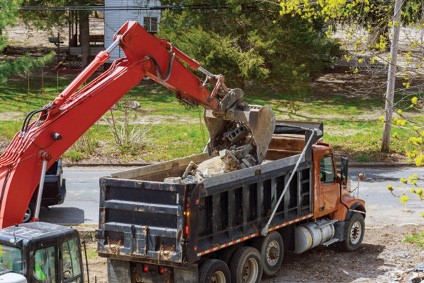
When a container arrives, the customer expects it to do its job, and protection against environmental damage is undoubtedly part of that. Containers are designed, constructed and tested at the time of manufacture to ensure they meet standards recommended by the Carboline Protective Coatings, as well as DOT specifications. Companies also are required to follow stringent guidelines to ensure roll-off containers position their customers to best protect the environment.
Testing is conducted throughout the development of the product. Before any coating is applied, the interior surfaces of the tank are inspected. Engineers should work to remove all existing blisters, weld splatters, sharp projections, slivers and pits. Meanwhile, decontamination typically is performed by combining rounding, grinding and high-pressure washing with sand injection. After the preliminary inspection, surface preparation begins. All oil and grease should be removed from the surfaces to be coated with a suitable safety solvent before abrasive blasting. Manufacturers also should take several steps to ensure they meet standards, from the type of air compressor used to coat the exterior to the anchor pattern’s depth or “tooth” in the metal.
Following the coating application and curing of the container, final testing begins. Before an order leaves the warehouse, all containers should be water tested to ensure they are liquid-tight and sift-proof. DOT terminology requires a “sift-proof non-DOT specification cargo tank and portable tank” and a “non-DOT specification cargo tank and portable tank suitable for [the] transport of liquids.”
Overall, meeting regulatory requirements is not only a form of compliance but also an opportunity for the owner/operator to protect the environment. Stormwater runoff wreaks havoc on water sources, and these chemical contaminants can harm not only the health of humans but also of wildlife. By using a container that works to prevent stormwater runoff and prioritizing ongoing maintenance and timely replacement, the industry can adequately do its part to keep the nation’s waters clean.
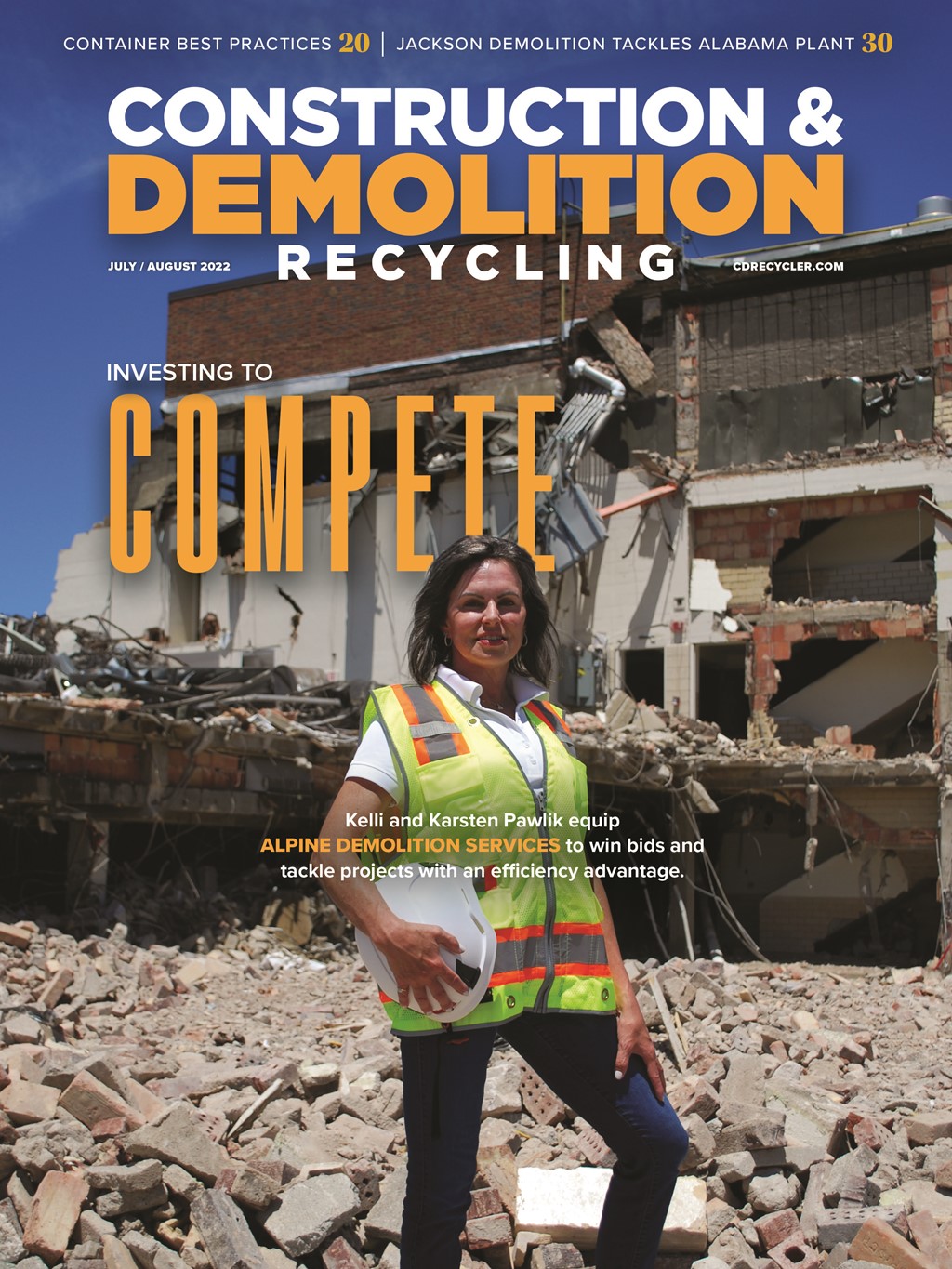
Explore the July August 2022 Issue
Check out more from this issue and find your next story to read.
Latest from Construction & Demolition Recycling
- Connect Work Tools names new service manager
- Architects’ billings slow, contractors stay busy into summer
- RMDAS figures show ferrous still in a trough
- Mt. Diablo receives RCI certification at Pittsburg, California, C&D facility
- Plastics recycling company wins top prize at NextCycle Colorado Pitch Competition
- Arena-sized venue is demolition target in Alabama
- Brandt scrap handlers available through Murphy Tractor
- Hendrickson celebrates Tiremaax installation milestone